Vinyl Siding 101 – How Vinyl Siding is Manufactured
Vinyl Siding
A Step-by-Step Guide: How Vinyl Siding is Made and Installed
Introduction: Vinyl siding has become popular for homeowners due to its durability, low maintenance requirements, and aesthetic appeal. Understanding how vinyl siding is manufactured and installed can help you make informed decisions about its use for your home. In this article, we will provide a comprehensive, easy-to-understand guide on the process of making and installing vinyl siding.
Manufacturing Vinyl Siding
Material Selection:
- The primary component of vinyl siding is polyvinyl chloride (PVC), a synthetic plastic polymer.
- Other additives such as colorants, stabilizers, and modifiers are mixed with PVC to enhance its properties.
Extrusion:
- The manufacturing process begins with a process called extrusion.
- The PVC compound is fed into an extruder machine, which heats and melts the material to a molten state.
- The molten PVC is then forced through a shaping die, forming it into the desired profile of the vinyl siding.
Cooling and Cutting:
- After passing through the shaping die, the extruded vinyl siding cools down rapidly.
- It moves through a water bath or cooling chamber to solidify and maintain its shape.
- Once cooled, the vinyl siding is cut into the desired lengths, typically 10 to 24 feet.
Finishing Touches:
- During the manufacturing process, various textures and patterns can be embossed onto the surface of the vinyl siding to mimic the appearance of wood grain or other textures.
- Color is added to the vinyl siding by incorporating pigments into the PVC compound.
- Protective coatings may also be applied to enhance durability and resistance to fading.
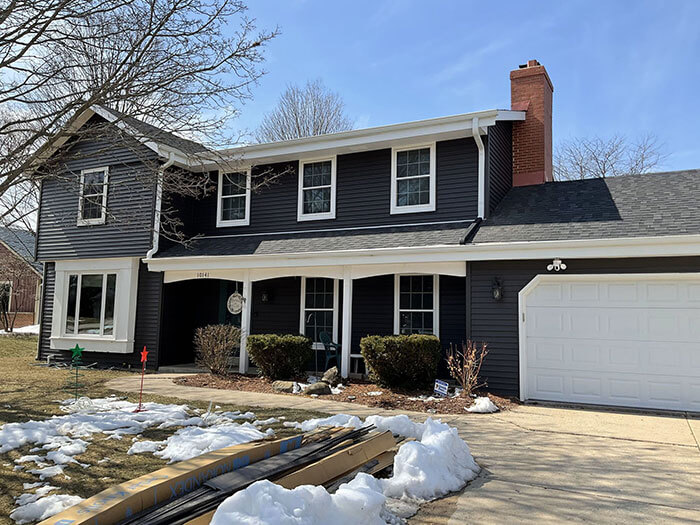
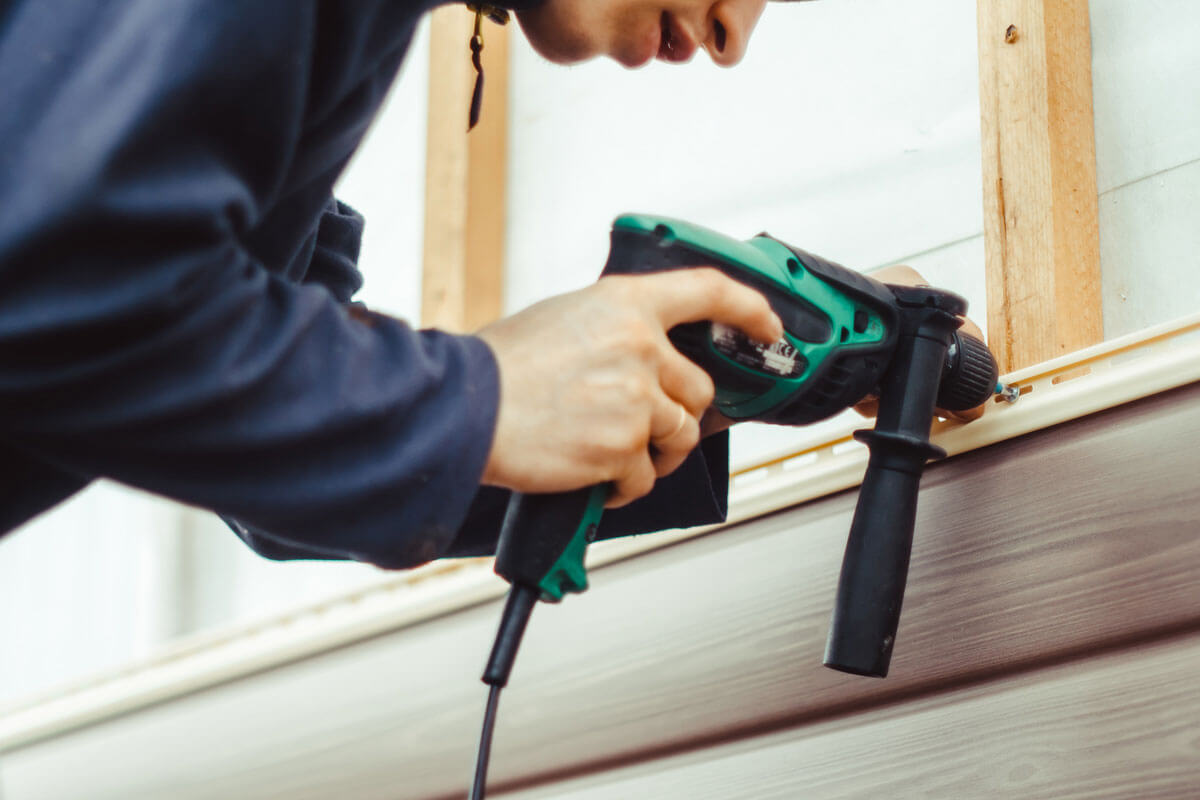